Understanding the Importance of Lathe Parts Factories in Metal Fabrication
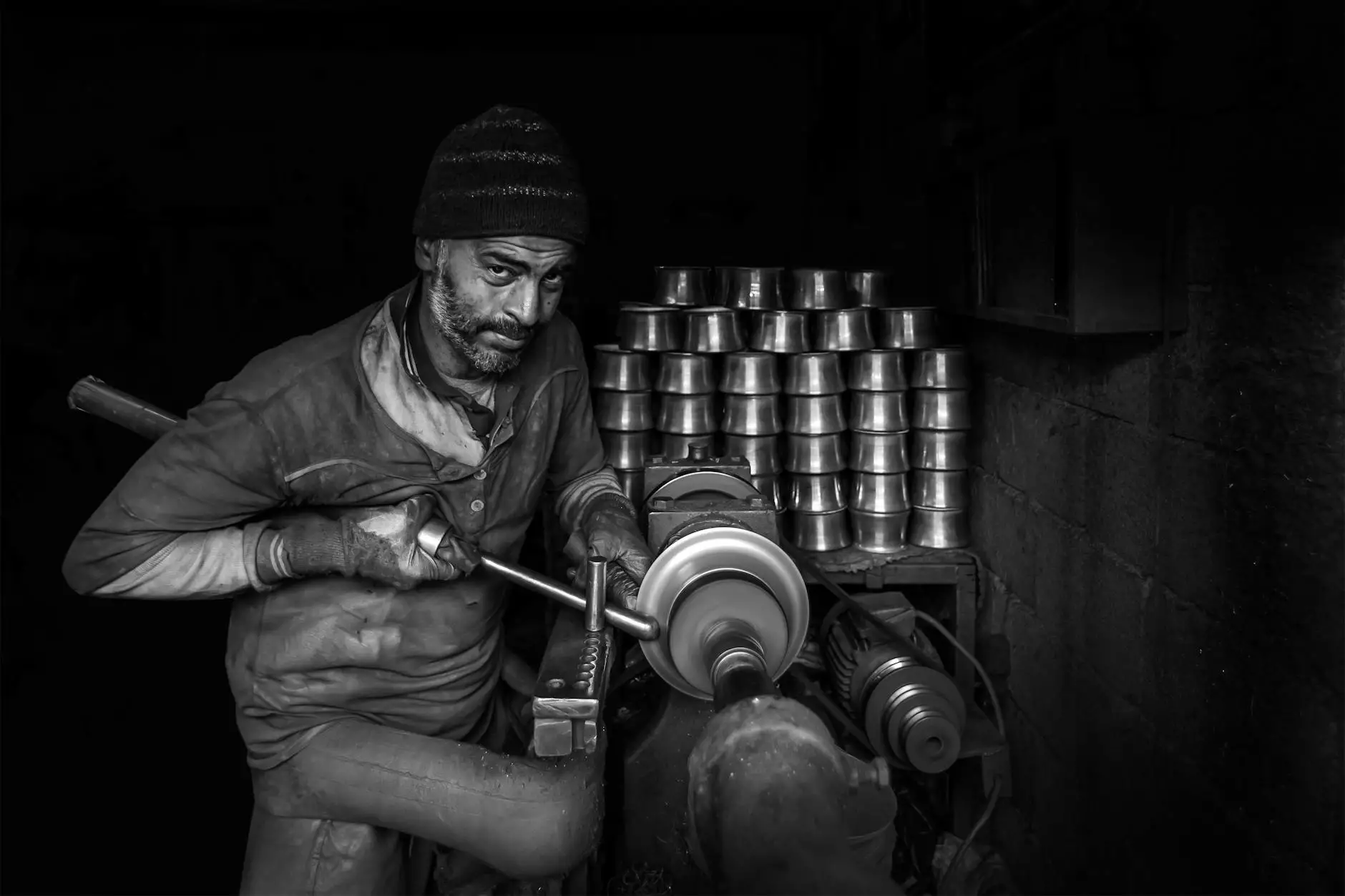
The realm of metal fabrication has undergone significant advancements, and at the heart of this evolution lies the crucial role played by lathe parts factories. These factories specialize in producing components that are essential for a wide array of industries, from automotive to aerospace. Their ability to create high-quality, precise lathe parts not only drives productivity but also enhances the overall quality of metalworking projects.
The Role of Lathe Parts Factories
Lathe parts factories are specialized manufacturing units that focus on creating components used in lathes. Lathes are machines that rotate a workpiece against a stationary cutting tool, allowing for the shaping of various materials. The ability to produce components with precision makes the role of lathe parts factories indispensable in many sectors.
Key Components Manufactured
Among the numerous parts produced, the following are vital:
- Spindles: The spindle is a critical component that rotates the workpiece.
- Chucks: These hold the workpiece securely in place.
- Tool Posts: This holds the cutting tools and allows for precise adjustments.
- Carriages: They enable the movement of the cutting tool along the longitudinal axis of the lathe.
- Bedways: These form the foundation of the lathe, providing support and alignment.
The Manufacturing Process at Lathe Parts Factories
The manufacturing process within a lathe parts factory involves several intricate steps, ensuring that every component meets the rigorous demands of modern engineering.
1. Material Selection
The first step in the manufacturing process involves selecting the right materials. Common materials used include:
- High-grade steel
- Aluminum alloys
- Copper and brass
- Plastic and composite materials for specific applications
Each material has its unique properties, making it suitable for specific lathe parts based on strength, durability, and weight requirements.
2. Precision Machining
Once the materials are selected, they undergo precision machining. This is where the magic happens. Modern lathe parts factories utilize advanced CNC (Computer Numerical Control) machines that allow for extremely accurate cuts and shapes to be achieved. The advantages of CNC machining include:
- High Precision: CNC machines can create parts with tolerances of just a few microns.
- Automation: This reduces human error and increases production speed.
- Complex Design Capability: CNC allows for the manufacturing of intricate shapes and designs that are not possible with traditional methods.
3. Quality Assurance
No lathe part leaves the factory without undergoing rigorous quality assurance testing. This ensures that every piece meets strict industry standards and customer specifications. Quality control measures typically include:
- Visual Inspections: To check for surface imperfections.
- Dimensional Checks: Utilizing micrometers and calipers for precision.
- Material Testing: To confirm the strength and durability of materials used.
Importance of Quality in Lathe Parts Manufacturing
The quality of lathe parts produced in a lathe parts factory is paramount. High-quality components lead to enhanced functionality, longer lifespans of the machines, and ultimately, higher satisfaction for end users.
Inconsistent or poorly manufactured lathe parts can lead to operational inefficiencies, machine breakdowns, and ultimately financial losses for manufacturers. Hence, investing in quality assurance systems is essential for any reputable lathe parts factory.
Industry Applications
Lathe parts manufactured in these factories serve a multitude of industries. Some prominent applications include:
Aerospace Industry
In aerospace, precision is critical. Every component must meet stringent safety and performance standards. Lathe parts are crucial in the production of:
- Engine components
- Landing gear
- Structural elements
Automotive Sector
The automotive industry relies heavily on lathe parts for various components, including:
- Crankshafts
- Transmission housings
- Brake rotors
Medical Devices
In the medical field, precision components manufactured by lathe parts factories are essential for medical devices such as:
- Surgical instruments
- Implants
- Diagnostic equipment
Advancements in Lathe Parts Manufacturing Technology
The `lathe parts factory` sector has continuously evolved with technological advancements. Recent innovations have transformed traditional methods, producing highly efficient and precise components.
3D Printing
One of the most significant advancements in recent years has been the incorporation of 3D printing technology. This allows for the rapid prototyping of lathe parts and even the production of final components in some cases, particularly in creating complex geometries that were once impossible with conventional machining methods.
Automation and Robotics
Automation has led to increased productivity due to the ability to run machines continuously with minimal human intervention. Robotics in lathe parts factories can perform tasks such as:
- Loading and unloading parts
- Performing repetitive machining operations
- Conducting inspections post-production
Choosing the Right Lathe Parts Factory
For businesses looking to partner with a lathe parts factory like DeepMould.net, several factors must be considered to ensure quality and reliability:
- Experience: Look for factories with a proven track record in the industry.
- Technology: Ensure they use the latest machining technologies and quality control measures.
- Customization: Choose a factory that offers tailored solutions to meet specific project needs.
- Client Testimonials: Seek feedback from past clients to gauge reliability and service quality.
Conclusion
In conclusion, the significance of lathe parts factories in the metal fabrication industry cannot be overstated. They play a fundamental role in ensuring that various sectors operate smoothly through the provision of high-quality, precision-engineered components. As technology continues to evolve, these factories are poised to further enhance their capabilities, paving the way for even more innovations in manufacturing. Companies like DeepMould.net represent the cutting edge of this industry, committed to quality and excellence in every part produced.